Mission Statement
Sign and Consultant Company (S.A.C.)​ is a company with a goal to provide the best quality advice and service to any company in need of help in lean manufacturing. S.A.C. is driven to make your company the most organized & successful in your area.
Our Process
I'm a paragraph. Click here to add your own text and edit me. It’s easy.
Just click “Edit Text” or double click me to add your own content and make changes to the font.
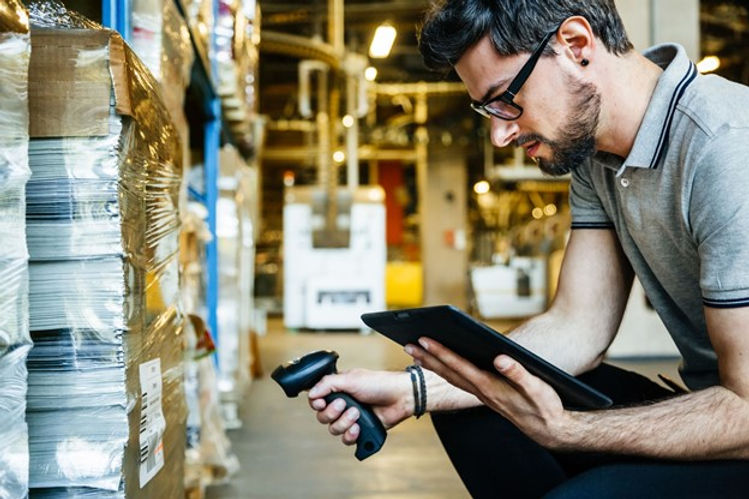
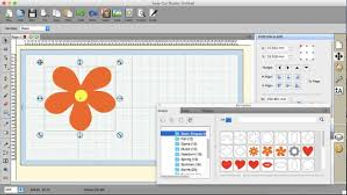
Draft & Design
Using computer software to design the most complex designs to exceed our customer expectations.

Hablamos Español
An advantage with SAC is that we are
bilingual so we are able to interact with
the workforce English or Spanish speaking. This allow us to understand their needs and train them well.

Design & Construction
Skillful hands to prepare and inspect the products to ensure the highest quality is provided.

On-Site Consultations
We take the time to understand your problems and look for opportunities to help you to look for the solutions.

The Finishing Touches
we take proud of our work and we ensure that all our signs are made with care and the most quality process to deliver excellent results.
Our Quality Guarantee
In today’s competitive environment, smart companies are fueling growth through leaner operations. Adopting lean practices, which focus on the elimination of waste throughout the enterprise, create cost savings while establishing an environment of continuous improvement.
Many manufacturing facilities have opted to follow the path towards a “5S” workplace organizational methodology as part of a continuous improvement program or lean manufacturing process.
The 5S system is part of Toyota’s Lean Manufacturing methodology designed to reduce waste within a facility.
5S is typically the first step towards eliminating waste from manufacturing processes and eventually leads to improving bottom line results. 5S is a foundation of kaizen, which is the practice of continuous improvement based on certain guiding principles
The 5S philosophy is “a place for everything and everything in its place,” and helps to eliminate wasted time, wasted space and wasted inventory. Implementing 5S raises product quality and improves work productivity, resulting in lower costs and higher efficiencies.
The end result of a 5S implementation is a significant reduction in space needed for existing operations. Workers improve their workspaces by cleaning and organizing them. Tools and materials are labeled and stored in organized storage locations. Shelving and racks optimize the storage of items in a smaller footprint, helping to improve the order picking process by eliminating the need to search for items.
Don’t confuse the approach to 5S as a substitute for the whole lean philosophy. 5S is just one of the many steps involved with adopting a lean mindset and then turning it into a continuous improvement mentality for all members of the organization.